Effective chemical cleaning of heat exchangers is primarily based on maximizing flow rate through either an individual unit or several units in series. This requires knowing first the type of heat exchanger being cleaned (e.g., tubular or plate) and whether fouling has either restricted or fully impeded flow (e.g., small to large number of plugged tubes). Of course, knowing where in the process an exchanger is employed also helps address what kind of fouling to expect. This is important as certain types of fouling, such as coke deposition, will not be removed or impacted by chemical cleaning. Where possible, this issue can be verified with testing of pulled sample deposits.
Once these parameters are established, a chemical cleaning program is developed to mitigate the fouling deposits. This is done in tangent to calculating the estimated volumes and flow rates required to achieve turbulent flow and deposit erosion while assessing overall flow distribution. This process also considers operating and temperature conditions, the number and size of temporary cleaning connections, and whether any impediments to operations exist or can manifest. These are all key factors in ensuring successful chemical cleaning of heat exchangers. Should some of these factors not be met, then adjustments to the chemical cleaning program, such as maximizing chemical concentration and circulation time, is required to compensate.
Ultimately, a full assessment results in a chemical program such as the example shown below:
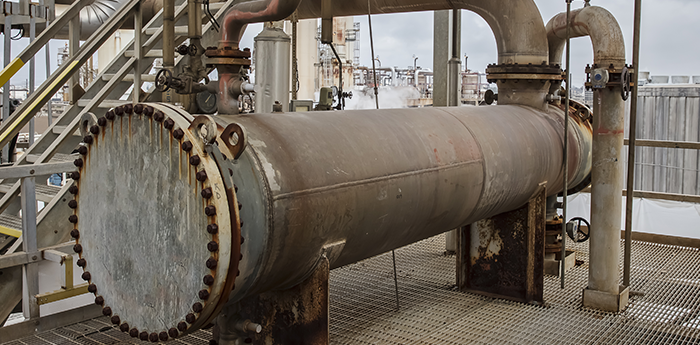