Reducing or eliminating nitrogen gas purging in catalyst decontamination procedures requires review of alternative application methods for removing hydrocarbon fouling along with the corresponding hydrocarbon and hydrogen sulfide gases. For reactor units where the introduction of moisture presents no issue, two phases of product application via vapour phase co-injection can be completed during maintenance and change-out activities.
Phase One – Oil & Hydrogen Sulfide Gas Removal
Phase one of the vapor phase co-injection would apply RAMSOL HD into the steam line to create an oil-in water emulsion-type aerosol. The aerosol predicted to act as an in-situ degreasing solution upon collection and condensation onto internal surfaces. Hydrogen sulfide gas abatement would then be achieved in the oil-phase with the hydrogen sulfide gas scavenging ingredient included in the formulation. During this stage, some LEL/hydrocarbon gas suppression/absorption is expected.
Primary components for monitoring job completion would involve monitoring the amount of hydrocarbon versus water in the sample solution and checking for and measuring hydrogen sulfide gas emissions in the sample headspace. The goals for these components lying in determining if hydrocarbon removal is reaching a maximum or receding and whether efficient sweetening is being achieved. Gas monitoring at the unit along with the results in this phase would thus dictate rates of injection for phase two.
Phase Two – Residual Oil-Skim, LEL/Hydrocarbon and Hydrogen Sulfide Gas Removal
Phase two of the vapor phase co-injection would apply ROC 60VP into the steam line to pull out residual oil-skim, absorb LEL/hydrocarbon gases and irreversibly remove remaining hydrogen sulfide gas in the aqueous phase. It is expected that this stage will be minimal in volume requirement in comparison to phase one and is intended to provide final job completion including water-film drainage/breakage and surface drying.
Primary components for monitoring job completion would involve monitoring the amount of hydrocarbon versus water as well as chemical in the sample solution and checking for and measuring hydrogen sulfide and hydrocarbon gas emissions in the sample headspace. The goals for these components lying in determining if hydrocarbon removal is reaching a maximum or receding and whether additional chemical is required, and whether efficient sweetening and gas absorption is being achieved. Gas monitoring at the unit along with the results in this phase would thus dictate cessation of chemical injection and duration of additional steam out to remove residual chemical.
The use of product via steam injection is expected to improve LEL suppression efficiency while ultimately removing contaminants from the system, as opposed to merely displacing them further downstream. The proposed adjustment to the procedure is also expected to reduce nitrogen gas purging and ultimately scheduling requirements.
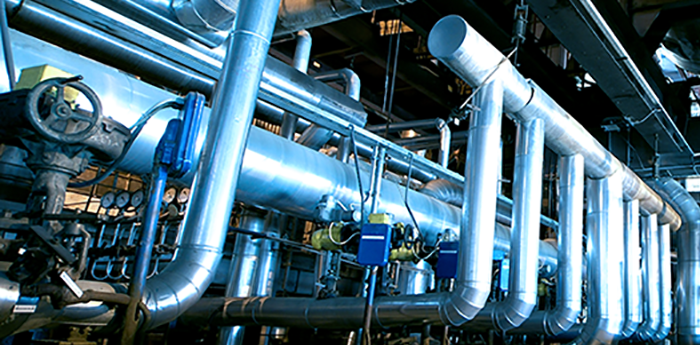