The primary goal of post-operational cleaning in refinery and petrochemical plants is to decontaminate and degas a unit or process vessel. This involves removing bulk foulant and solid debris from the unit while simultaneously freeing it of hazardous gas contaminants. This process is completed during shutdowns or turnarounds to provide fast, efficient, and safe entry for purposes of maintenance or inspection.
To accomplish this goal, procedures need to be developed that implement either a liquid circulation or a vapor-phase co-injection to distribute a chemical cleaning product inside the unit. Other methods of application exist, including purging or foam blanketing, but they tend to target only gas contaminants. Regardless of method, the procedure must apply the appropriate chemistries is such a way as to promote both efficient and effective operations and schedules in the decontamination and degasification process.
Efficient and effective application of a chemical cleaning program may involve a single-step, multi-step, or combinational process. A single-step procedure involves the injection of only one chemical product at various injection points. Multi-step procedures involve the injection of a sequence or progression of chemical products to mitigate fouling and contamination issues alleviated by products not fully compatible upon direct mixing. That is, they may neutralize each other, cause degradation and loss of activity, etc. This procedure typically occurs at one main injection point. Combinational procedures involve injecting more than one chemical product to mitigate fouling and contamination issues that can be remediated by products capable of being mixed at the point of application. The latter two procedures are adopted when complex fouling is present or when a one-pack product lacks the activity to address higher degrees of fouling or gas contamination.
Overall, combined with sufficient heat and agitation, a proper chemical cleaning program will assist in full dissolution of the bulk contamination. Typically, the product or products will be chosen when the contamination has been characterized and located within the vessel or unit. The method of application, as discussed above, will have some influence in this choice as well.
Some of the products to review for removing bulk solids and contaminants are listed below with a brief description:
- PENBLITZ 688L – alkaline degreaser concentrate used for mobilizing asphaltenes, iron sulfide and sludge residuals in liquid circulation procedures
- CITRIKLEEN HD – industrial degreaser used for various metal surface cleaning applications in both liquid circulation and vapor-phase co-injection procedures
- RAMSOL BCX – solvent degreaser used for mobilizing asphaltenes and resins in liquid circulation procedures
- RAMSOL HD – solvent degreaser used in nitrogen purge procedures requiring the removal of hydrocarbon sludge and H2S
Some of the products to review for targeting a spectrum of gas contaminants are listed below:
- ROC 40 – enzyme-based cleaner and degasification aid
- ROC 45 – surfactant-based cleaner and degasification aid
- ROC 60VP – high-temperature stable hydrogen sulfide scavenger and degasification aid
All the products will assist in mitigating benzene, LEL, and H2S as well as iron sulfides. When applied at the appropriate concentration, the degassing product line produces a micellar solution that allows for higher solubility of hydrocarbon gases into the bulk liquid. Models suggest that high mol fractions of low molecular weight gases can be captured translating to approximately 400-600 ppmv per liter of micellar solution.
Should hydrogen sulfide present the more significant hazard, products to review for targeting it are listed below with a brief description:
- SCAVEX – sulfide scavenger useful for chemical circulation procedures in combination with ROC products or on its own in a single-step application.
- SCAVEX VP – thermally-stable sulfide scavenger useful for high temperature applications or circulations as well as in vapor-phase co-injection
- SCAVEX AG – acid-stable sulfide scavenger and alternative to triazine and formaldehyde-based formulations
Once a method of application and an appropriate product listing has been identified, procedure development is initiated in line with the stakeholder’s desired or expected outcomes.
This process involves a thorough risk assessment to lay out the necessary steps required to complete the chemical cleaning efficiently and effectively. The complete process is outlined below:
- Risk Assessment
- Hazards review – e.g., hot liquids, compatibility, burns/spills, toxic vapors, or oxygen deficiency at vent points, etc.
- Steps to mitigate operational hazards
- Method Assessment & Procedure Development
- Vessel survey – PID’s, foulant location, previous products and method of application employed, previous cleaning results, etc.?
- Foulant characterization – is a sample available for solubility testing?
- Gas contaminants – e.g., estimated or measured concentrations?
- Method Implementation –appropriate injection and drainage points, identification of circulation loops, sampling points, etc.
- Retain monitoring – periodic detection of contaminants, product concentration, etc.
- Disposal Assessment
- Waste restrictions – water treatment, disposal, etc.
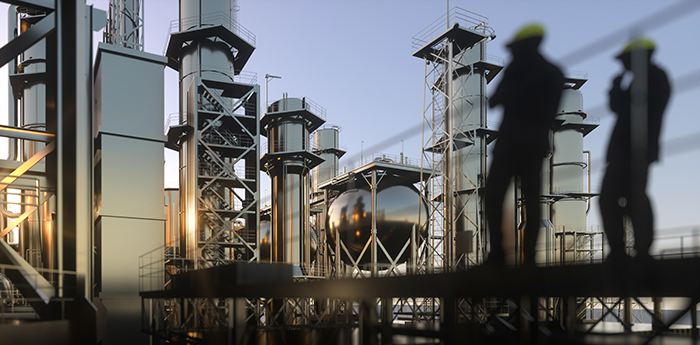