Industrial process fouling can often be variable or complex, depending on the industrial process that produced it. This variability stems from numerous factors including variations in the feedstock being processed, effects of temperature gradients, internal surface integrity of the processing unit, the processing unit’s length of time in operation, and more. Effective removal of this process fouling therefore requires functionally characterizing this variability by breaking the fouling down to its compound constituents.
Breaking down process fouling into its compound constituents is the first step in effective solubility testing. This is often accomplished either through thermogravimetric testing or solvent extraction of representative samples to determine the balance between:
- Volatiles – compounds that can either boil off or evaporate during the chemical cleaning process. Excessive volatiles can indicate a potential need for emissions monitoring and control. A large loss of volatile material can also cause or create changes in the fouling deposits during the initial stages of the chemical cleaning process.
- Soluble Organics – compounds that are readily water or oil soluble. These compounds are more easily targeted by conventional chemical cleaning programs and procedures.
- Insoluble Organics – high molecular weight, high boiling point compounds that are often less if not completely insoluble in water or oil-based solvents. High enough amounts of insoluble compounds can be the difference between an effective chemical cleaning program and the need to implement mechanical cleaning procedures.
- Inorganics – compounds readily soluble in water or responsive to acid immersion. High amounts of inorganic fouling may suggest the necessity of a multi-stage cleaning procedure.
On rare occasions more specialized testing such as simulated distillation or x-ray diffraction (XRD) is required to further characterize the fouling and verify if chemical cleaning is a viable approach or requires supplementation by mechanical processes such as high-pressure water blasting.
Constituent breakdown such as this helps to target the appropriate chemical cleaning program required to expedite removal of the process fouling from the unit or vessel of interest through direct solubilization. Evaluating ratios of fouling to chemical cleaning solution at various durations also helps with predicting or estimating the minimum duration of the chemical cleaning operation.
These services are all included in West Penetone’s solubility testing program and standardized in technical reports to provide insights on how to structure the chemical cleaning project.
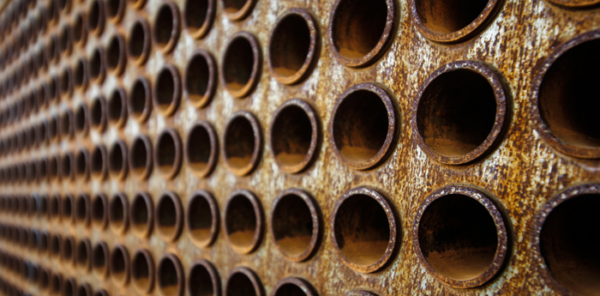