Degassing or degasification is a colloquial term used in the chemical cleaning industry to describe the process of removing hazardous gas contaminants, such as H2S, BTEX, or other low molecular weight hydrocarbon gases, from process units or vessels found in the oil and gas industry. These contaminants create a variety of health and physical safety hazards and prevent personnel from completing maintenance operations. To complete these operations safely and efficiently, these vessels must first be “shutdown” and put through a chemical cleaning process to remove the contaminants.
An effective cleaning process will serve to actively mix this hazard gas mixture with a surfactant solution. The appropriate surfactant solution then serves to solubilize these gases and low molecular weight vapors into micellar aggregates. This process is also known as micellar solubilization or encapsulation and is depicted int the figure below.
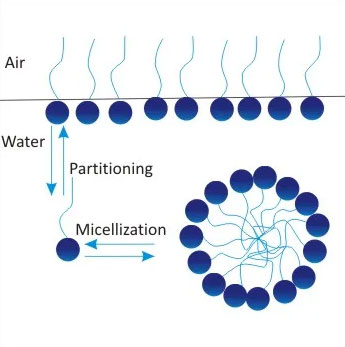
Figure 1: Aqueous phase behavior of surfactants. When above certain concentrations produce micelles or micellar aggregates. Note the solubilization of hydrophobic particles within the micelle.
The overall efficiency of this process is dependent on several factors including boiling point and vapor pressure of the gas particles and the type of hydrophobic groups present within the surfactant molecules or mixture.
Research at West Penetone has found products like ROC 40 can enhance solubility of high vapor pressure gases up to 20% by weight while also effectively emulsifying high boiling point vapors and neutralizing hydrogen sulfide gas. When accounting for vapor pressure and density differences on an equivalent mass by cubic meter basis, this translates to more efficient management of hazardous gas mixtures with 10-20% LEL contamination compared to water flushing or steam purging alone.
Other products in the ROC product line also offer additional features not limited to residual odor-masking (e.g., PINKROC), increased emulsification capacity (e.g., ROC 45), high capacity H2S removal (e.g., ROC 55X), or high-temperature application (e.g., ROC 60VP).
Case histories of ROC product line applications can be found in our Knowledge Center.
Of course, the chemical cleaning process overall requires an appropriate method of application for dispersing product as well as the implementation of effective job monitoring procedures. These aspects all being a part of the S.T.AR. program.
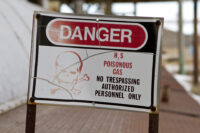